Design technologies drone represent a rapidly evolving field, pushing the boundaries of engineering, software, and materials science. From the sophisticated software used for design and simulation to the advanced manufacturing techniques employed in their production, drones are a testament to human ingenuity. This exploration delves into the multifaceted world of drone technology, examining the intricate interplay of design, manufacturing, and operational systems that define these versatile aerial platforms.
We will journey through the core components of drone systems, including flight control, propulsion, power systems, communication protocols, and imaging technologies. We’ll also investigate the crucial role of materials science and software development in shaping drone capabilities, as well as the exciting possibilities of integrating drones with other cutting-edge technologies such as AI and IoT. Finally, we will speculate on future trends and advancements expected in this dynamic field.
Drone Design Software & Platforms
The design and simulation of drones require specialized software capable of handling complex aerodynamic models, mechanical systems, and flight control algorithms. Several leading platforms cater to different needs and expertise levels, ranging from user-friendly interfaces for hobbyists to sophisticated tools for professional engineers. The choice of software often depends on the complexity of the drone design, budget constraints, and the user’s familiarity with CAD software.
The capabilities of drone design software extend beyond simple 3D modeling. These platforms often incorporate physics engines for realistic flight simulations, allowing designers to test and refine their designs virtually before physical prototyping. This iterative design process reduces development time and costs, and ultimately leads to more efficient and reliable drone systems.
Leading Drone Design Software Platforms
Several software packages dominate the drone design landscape. Pix4Dmodel, for example, excels in photogrammetry and 3D modeling from drone-captured images, ideal for creating detailed terrain maps and models. Other platforms, like QGroundControl, focus on mission planning and flight control, providing tools to program autonomous flights and analyze flight data. For comprehensive design and simulation, professional-grade CAD software packages such as SolidWorks, Autodesk Fusion 360, and CATIA are frequently used. These offer advanced features for detailed mechanical design, finite element analysis (FEA), and computational fluid dynamics (CFD) simulations. The choice of platform often depends on the user’s experience level and specific design requirements.
Comparison of CAD Software Packages for Drone Modeling
SolidWorks, known for its robust features and industry-standard capabilities, provides extensive tools for detailed mechanical design, allowing for precise modeling of drone components like frames, motors, and propellers. Autodesk Fusion 360, a cloud-based platform, offers a more accessible and integrated design environment, combining CAD, CAM, and CAE functionalities. Its ease of use and collaborative features make it popular among hobbyists and small teams. CATIA, a high-end solution used in aerospace and automotive industries, offers advanced functionalities, including complex surface modeling and highly accurate simulations, but it requires significant expertise and is typically more expensive. The choice between these packages depends on the complexity of the drone design, the user’s skill level, and the available budget. For simple designs, Fusion 360 might suffice; for complex, high-performance drones, SolidWorks or CATIA might be necessary.
Design of a Fictional Drone using Autodesk Fusion 360
Let’s consider the design of a fictional surveillance drone, “The Argus,” using Autodesk Fusion 360.
The design process would begin with conceptualization, defining the drone’s purpose (surveillance), size constraints (compact for maneuverability), and key features (high-resolution camera, long flight time). Next, we would create a 3D model of the airframe, using Fusion 360’s sketching and modeling tools. This would involve designing the chassis, incorporating mounting points for the camera, battery, and other components. Then, we would design individual components like the motor mounts, propeller guards, and landing gear, ensuring proper fit and functionality. The process would continue with the integration of electronic components, including the flight controller, GPS module, and communication system. Finally, we would conduct simulations to assess the drone’s flight characteristics, stability, and overall performance. This would involve using Fusion 360’s simulation tools or integrating with external CFD and FEA software for more detailed analysis. The iterative nature of the design process would allow for adjustments and refinements based on simulation results, leading to an optimized design.
Drone Manufacturing Technologies
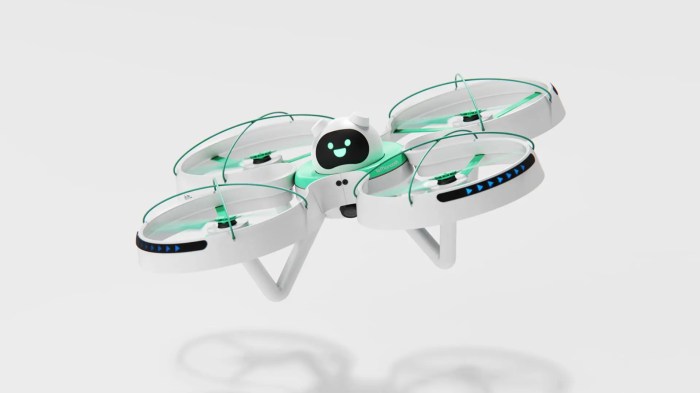
The manufacturing process of drones involves a complex interplay of various techniques, depending on the drone’s size, complexity, and intended application. From simple hobbyist drones to sophisticated military or commercial models, the manufacturing process adapts to meet specific requirements of performance, durability, and cost-effectiveness. A range of methods are employed, often in combination, to achieve the desired outcome.
Drone manufacturing utilizes a diverse set of techniques, each offering unique advantages and disadvantages. The selection of these techniques often depends on factors such as the drone’s design, the desired production volume, and budgetary constraints. This results in a dynamic manufacturing landscape, constantly evolving with advancements in materials science and production technologies.
Manufacturing Techniques Employed in Drone Production
Several key manufacturing processes are commonly used in drone production. These include CNC machining, injection molding, die casting, sheet metal fabrication, and increasingly, 3D printing (additive manufacturing). CNC machining provides precision for intricate parts, while injection molding allows for high-volume production of standardized components. Die casting is ideal for creating complex shapes with high strength, and sheet metal fabrication is efficient for creating lightweight, aerodynamic airframes. The choice depends heavily on the component and the overall design goals.
Advantages and Disadvantages of 3D Printing for Drone Components
3D printing, or additive manufacturing, offers significant advantages in drone production, particularly for prototyping and low-volume manufacturing. The ability to create complex geometries and customized designs with relative ease makes it a powerful tool. However, limitations exist in terms of production speed and material limitations compared to traditional methods.
Advantages include rapid prototyping, customized designs, reduced tooling costs, and the ability to produce lightweight and complex parts. Disadvantages include slower production speeds for large-scale manufacturing, limitations in material choices (especially for high-strength, high-temperature applications), and potential for lower surface finish quality compared to traditional machining techniques. The strength of 3D-printed parts can also be a concern depending on the material and printing technique. For instance, a 3D-printed PLA plastic drone may not be as robust as one made with injection-molded carbon fiber.
Comparison of Traditional and Additive Manufacturing for Drone Construction
The table below compares traditional manufacturing methods with additive manufacturing (3D printing) across key aspects of drone construction. Note that the values are generalized and can vary significantly depending on the specific materials, technologies, and production scale.
Manufacturing Method | Cost | Speed | Material Options |
---|---|---|---|
Traditional (e.g., Injection Molding, CNC Machining) | High initial tooling cost, lower per-unit cost for high volumes | High production speed for high volumes | Wide range, including plastics, metals, composites |
Additive Manufacturing (3D Printing) | Low initial cost, higher per-unit cost for low volumes | Slower production speed, ideal for prototypes and low volumes | More limited range, though expanding rapidly; plastics, some metals, composites |
Drone Flight Control Systems
Drone flight control systems are the brains behind autonomous flight, enabling drones to navigate and perform complex maneuvers. These systems integrate various hardware and software components to achieve stable and controlled flight, adapting to changing environmental conditions and pilot commands. Understanding their functionality is crucial for designing, building, and operating safe and effective drones.
The core functionality of a drone flight control system involves receiving input from various sensors, processing this data, and then sending commands to the drone’s actuators (motors and propellers) to maintain stability and execute flight instructions. This intricate process is achieved through a sophisticated interplay of hardware and software components.
Key Components of a Drone Flight Control System
A typical drone flight control system comprises several essential components working in concert. These include a flight controller, various sensors (like an Inertial Measurement Unit (IMU) and GPS), and the actuators (the motors and propellers). The flight controller acts as the central processing unit, receiving data from the sensors, executing flight algorithms, and sending control signals to the motors. The sensors provide real-time information about the drone’s position, orientation, and movement, while the motors translate the flight controller’s commands into physical motion. The entire system relies on continuous feedback loops to ensure precise control.
The Role of Sensors in Drone Navigation
Sensors play a pivotal role in enabling drones to navigate effectively. The IMU, a crucial sensor, measures the drone’s angular velocity and linear acceleration, providing data about its orientation and movement in three-dimensional space. This data is essential for maintaining stability and executing precise maneuvers. GPS, on the other hand, provides information about the drone’s geographical location, allowing it to navigate to specific coordinates or maintain a fixed position. Other sensors, such as barometers (measuring altitude) and magnetometers (measuring magnetic field direction), contribute to more accurate positioning and stability. The integration of these sensor readings allows the flight controller to create a comprehensive picture of the drone’s state and adjust its control signals accordingly. For example, if the IMU detects a sudden tilt, the flight controller can adjust motor speeds to correct the drone’s orientation.
Simplified Block Diagram of a Drone Flight Control System
A simplified block diagram would illustrate the flow of information as follows: The diagram would show various sensor blocks (IMU, GPS, barometer, magnetometer) feeding data into a central flight controller block. The flight controller block would then process this data using algorithms to determine the necessary control actions. These control actions are then sent to the motor control block, which adjusts the speed and direction of the individual motors. Finally, feedback loops from the sensors would continuously provide updated information to the flight controller, ensuring a closed-loop control system. This constant feedback allows for real-time adjustments to maintain stability and execute the desired flight path. The diagram would visually represent this closed-loop system, highlighting the continuous flow of information and control signals.
Drone Propulsion Systems
Drone propulsion systems are the heart of any unmanned aerial vehicle (UAV), dictating its flight characteristics, payload capacity, and operational range. The choice of propulsion system significantly impacts the overall design and performance of the drone, making it a critical consideration in the development process. Understanding the different options available and their respective advantages and disadvantages is crucial for selecting the optimal system for a given application.
The selection of a propulsion system hinges on a complex interplay of factors, including the desired flight time, payload capacity, maneuverability, operating environment, and cost considerations. Different applications demand different performance characteristics. For instance, a surveillance drone requires long endurance, while a delivery drone prioritizes payload capacity and speed. These diverse needs necessitate a variety of propulsion solutions.
Types of Drone Propulsion Systems
Drone propulsion systems broadly fall into two categories: electric and hybrid. Electric propulsion systems are the most common, utilizing electric motors powered by batteries. These offer simplicity, quiet operation, and relatively low maintenance. Hybrid propulsion systems combine electric motors with internal combustion engines (ICEs) or fuel cells, aiming to extend flight times and increase payload capacity beyond the limitations of battery technology alone. However, they are typically more complex and heavier than purely electric systems.
Factors Influencing Propulsion System Selection
Several key factors influence the choice of a propulsion system for a specific drone application. These include:
- Mission Requirements: The primary function of the drone dictates the needed flight time, speed, payload capacity, and maneuverability. A long-range surveillance drone requires a high-efficiency propulsion system for extended flight, whereas a racing drone prioritizes speed and agility.
- Payload Capacity: Heavier payloads necessitate more powerful motors and larger propellers, often leading to increased energy consumption and reduced flight time. The relationship between payload and propulsion system is directly proportional.
- Operating Environment: Environmental factors such as wind conditions, temperature extremes, and altitude can significantly impact propulsion system performance. For example, drones operating at high altitudes require systems optimized for thin air.
- Cost and Maintenance: Electric propulsion systems generally have lower initial costs and maintenance requirements compared to hybrid systems. However, battery replacement costs can be a significant factor over the lifespan of the drone.
- Safety and Regulations: Safety regulations and standards influence the choice of propulsion systems, particularly concerning the use of fuels and the potential for hazards.
Motor and Propeller Combinations
The choice of motor and propeller significantly impacts the performance and efficiency of the drone. Different motor types (e.g., brushless DC motors, brushed DC motors) offer varying power outputs, efficiencies, and costs. Propeller design (e.g., diameter, pitch) influences thrust, speed, and efficiency. Optimizing the motor and propeller combination for a specific drone size and payload is critical for achieving desired performance.
- Small Drones (e.g., hobbyist drones): These often use smaller, lighter motors and propellers, prioritizing efficiency and maneuverability over raw power. A common example would be a small quadcopter using brushless DC motors with relatively low kV ratings and small, lightweight propellers.
- Medium-Sized Drones (e.g., delivery drones): These drones require a balance between power, payload capacity, and efficiency. They may utilize larger brushless DC motors with higher kV ratings and larger propellers to lift heavier payloads. A specific example might be a delivery drone employing motors capable of delivering 1kg+ of payload.
- Large Drones (e.g., heavy-lift drones): These typically use powerful motors and large propellers to lift substantial payloads. The motors might be custom-designed or utilize multiple motors for redundancy and improved power distribution. Examples include drones used for construction or infrastructure inspection, often utilizing multi-rotor configurations with high-torque motors.
Drone Power Systems and Battery Technology
The power system is arguably the most critical component of any drone, dictating its flight time, payload capacity, and overall performance. The evolution of battery technology has directly impacted the capabilities and widespread adoption of drones, transforming them from niche research tools to versatile platforms used across numerous industries. This section explores the advancements in drone power systems and battery technology, comparing various battery types and designing a hypothetical power system for a specific drone application.
The development of drone power systems has closely followed advancements in battery technology. Early drones relied heavily on bulky and relatively low-capacity Nickel-Cadmium (NiCd) and Nickel-Metal Hydride (NiMH) batteries. These technologies, while readily available, suffered from short lifespans, the memory effect (in NiCd), and relatively low energy density. The advent of Lithium Polymer (LiPo) batteries revolutionized the drone industry. Their higher energy density, lighter weight, and improved cycle life enabled longer flight times and the development of smaller, more agile drones. More recently, research into solid-state batteries and other advanced technologies promises even further improvements in safety, energy density, and lifespan.
Battery Technology Comparison
The choice of battery type for a drone depends on several factors including flight time requirements, payload capacity, cost, and safety considerations. Below is a comparison of common battery types used in drones:
Battery Type | Energy Density (Wh/kg) | Lifespan (Cycles) | Advantages | Disadvantages |
---|---|---|---|---|
Lithium Polymer (LiPo) | 150-250 | 300-500 | High energy density, lightweight, high power output | Safety concerns (flammability), voltage sag under high load, requires careful charging and storage |
Lithium Iron Phosphate (LiFePO4) | 100-150 | 2000+ | High safety, long lifespan, robust performance | Lower energy density compared to LiPo, higher weight |
Nickel-Metal Hydride (NiMH) | 60-80 | 500-1000 | Relatively inexpensive, readily available | Lower energy density, shorter lifespan compared to LiPo |
Hypothetical Drone Power System Design
Let’s design a power system for a hypothetical agricultural drone tasked with crop spraying. This drone requires a flight time of approximately 30 minutes, a payload capacity of 10kg (including the spray tank), and needs to maintain stable hovering capabilities. Considering these requirements, a LiPo battery is a suitable choice due to its high energy density, enabling a relatively compact and lightweight power system.
We’ll specify the following:
* Battery Type: Lithium Polymer (LiPo)
* Battery Capacity: A 22.2V, 10000mAh (10Ah) LiPo battery provides a good balance between flight time and weight. This capacity, combined with an efficient power system, should easily achieve the 30-minute flight time requirement. This is based on estimates from similar agricultural drones currently in use, which typically require batteries in this range for similar operational demands. For instance, the DJI Agras MG-1P uses a battery pack with a similar capacity for comparable operations.
* Power Requirements: The drone’s motors, flight controller, and payload system will have varying power demands. We can estimate the total power draw based on similar drone designs and adjust this based on real-world testing. A conservative estimate for peak power draw might be around 1000W, requiring the battery management system to efficiently handle this demand. The specific power draw will depend on the motors chosen and the flight conditions. However, this 1000W figure is a reasonable starting point for design and further testing and refinement will be needed.
The overall power system will also include a Battery Management System (BMS) to monitor cell voltage, current, and temperature, ensuring safe operation and preventing overcharging or discharging. A suitable power distribution board will be needed to efficiently distribute power to the various components of the drone.
Drone Communication Technologies
Effective communication is paramount for safe and efficient drone operation. Reliable data transmission and control signals are crucial for autonomous flight, real-time data acquisition, and overall system performance. This section explores the various communication protocols employed in drone technology, the challenges inherent in maintaining consistent connectivity, and a comparison of the capabilities of different communication systems.
Drone communication systems facilitate the two-way exchange of information between the drone and its ground control station (GCS). This encompasses control commands sent from the GCS to the drone, and telemetry data – including position, altitude, battery level, and sensor readings – transmitted from the drone back to the GCS. The choice of communication protocol significantly impacts the drone’s range, data rate, latency, and overall reliability.
Communication Protocols Used in Drone Control and Data Transmission
Several communication protocols are used for drone control and data transmission, each with its own strengths and weaknesses. These protocols differ in their range, data rate, security features, and susceptibility to interference. Common protocols include WiFi, Bluetooth, Zigbee, and cellular technologies (like 4G/5G). Proprietary systems are also utilized by some manufacturers.
Challenges of Maintaining Reliable Drone Communication
Maintaining reliable communication in diverse environments presents significant challenges. Factors such as distance, terrain, atmospheric conditions, and interference from other radio sources can severely impact signal quality and connectivity. Obstructions like buildings, trees, and mountains can attenuate or block signals, leading to signal loss or increased latency. Multipath propagation, where signals reflect off multiple surfaces, can cause signal distortion and interference. Furthermore, radio frequency (RF) interference from other devices operating on the same or adjacent frequencies can disrupt communication. Adverse weather conditions, such as heavy rain, snow, or fog, can also significantly degrade signal quality.
Comparison of Range and Data Rate Capabilities of Different Communication Systems
Different communication systems offer varying ranges and data rates. WiFi, while offering relatively high data rates, typically has a limited range, suitable primarily for short-range operations in line-of-sight conditions. Cellular networks, such as 4G LTE and 5G, provide significantly longer ranges but often at the cost of lower data rates compared to WiFi, depending on network infrastructure and signal strength. The trade-off between range and data rate is a critical consideration when selecting a communication system for a specific drone application. For instance, a drone used for aerial photography might prioritize high data rates for real-time image transmission, while a drone used for long-range surveillance might prioritize extended range over high data rates. The use of dedicated long-range communication systems, such as LoRaWAN, can extend the operational range but with a significant reduction in data rate. This makes it suitable for applications that require infrequent updates or only transmit small data packets.
Drone Imaging and Sensing Technologies
Drone-mounted sensors significantly expand the capabilities of unmanned aerial vehicles (UAVs), transforming them into powerful platforms for data acquisition across numerous industries. These sensors provide a unique perspective and level of detail unattainable through traditional methods, enabling efficient and effective data collection in diverse environments. This section details the key sensor technologies utilized in modern drones and their respective applications.
Camera Systems
Drone cameras range from simple RGB cameras to highly sophisticated multispectral and hyperspectral imaging systems. RGB cameras capture visible light, producing familiar color images widely used in aerial photography, videography, and visual inspection. Multispectral cameras capture images across multiple wavelengths beyond the visible spectrum, including near-infrared (NIR) and red-edge bands. This data is invaluable in precision agriculture for assessing crop health and identifying stress factors. Hyperspectral cameras take this a step further, capturing hundreds of narrow, contiguous spectral bands, offering even finer detail about the composition and characteristics of surfaces. The higher spectral resolution allows for the detection of subtle variations in vegetation, minerals, or other materials, enabling highly accurate analysis. For example, hyperspectral imaging can differentiate between healthy and diseased plants based on their unique spectral signatures, long before visual symptoms become apparent.
LiDAR Systems
Light Detection and Ranging (LiDAR) uses laser pulses to measure distances, creating highly accurate 3D point clouds of the terrain. These point clouds are then used to generate detailed digital elevation models (DEMs), orthomosaics, and other geospatial data products. LiDAR is particularly useful in applications requiring precise measurements of elevation, such as surveying, mapping, and infrastructure inspection. For instance, LiDAR can accurately map the topography of a construction site, allowing for efficient planning and execution of earthworks. Different types of LiDAR systems exist, including topo-LiDAR for terrain mapping and bathymetric LiDAR for underwater mapping. The choice of LiDAR system depends on the specific application and the required level of detail.
Thermal Imaging Systems
Thermal cameras detect infrared radiation emitted by objects, creating images based on temperature differences. This technology is useful in various applications, including building inspections (detecting heat loss), search and rescue operations (locating individuals), and precision agriculture (monitoring soil moisture and plant health). For example, a thermal camera can detect insulation deficiencies in a building by identifying areas of significant heat loss, helping to improve energy efficiency. In agriculture, thermal imaging can identify areas of water stress in crops, allowing for targeted irrigation. The sensitivity and resolution of thermal cameras vary, impacting the quality and detail of the acquired data.
Hypothetical Drone Sensor Payload for Agricultural Monitoring
A comprehensive agricultural monitoring drone would benefit from a multi-sensor payload combining the strengths of various technologies. This payload would include:
- A multispectral camera: Capturing data across visible and near-infrared wavelengths for vegetation indices calculations (NDVI, NDRE) to assess crop health and vigor.
- A thermal camera: Providing information on soil moisture, plant temperature, and identifying areas of stress due to drought or disease.
- A high-resolution RGB camera: Generating detailed images for visual inspection of crop growth and identifying any physical damage or weed infestations.
The rationale behind this sensor selection is to provide a holistic view of crop health and environmental conditions. The combined data from these sensors would allow farmers to make informed decisions regarding irrigation, fertilization, and pest control, optimizing resource use and maximizing crop yields. For example, the combined data could identify specific areas within a field requiring targeted irrigation based on both vegetation stress (multispectral) and soil moisture levels (thermal). This precision approach minimizes water waste and optimizes crop productivity.
Drone Materials Science and Engineering
The selection of materials is paramount in drone design, directly impacting performance, durability, and overall flight characteristics. The ideal material balances lightweight properties with exceptional strength and stiffness to maximize flight time and payload capacity while ensuring structural integrity. This necessitates a careful consideration of various material properties and their trade-offs.
The importance of lightweight yet strong materials in drone design cannot be overstated. A lighter drone requires less energy for flight, resulting in extended flight times and increased efficiency. Simultaneously, the materials must possess sufficient strength and stiffness to withstand the stresses and strains of flight, including vibrations, impacts, and aerodynamic forces. This delicate balance is crucial for achieving optimal performance and safety.
Material Properties for Drone Construction, Design technologies drone
Carbon fiber reinforced polymers (CFRP), aluminum alloys, and plastics are commonly used in drone construction. Each material exhibits unique properties influencing its suitability for specific drone components. Carbon fiber, known for its exceptionally high strength-to-weight ratio, is frequently used in airframes, providing structural rigidity while minimizing weight. Aluminum alloys offer a good balance of strength, stiffness, and cost-effectiveness, often utilized in components where higher impact resistance is needed. Plastics, particularly those reinforced with fibers, are employed in less structurally critical parts, offering lightweight and cost-effective solutions.
Comparison of Material Performance Characteristics
Material | Strength | Stiffness | Weight | Cost | Impact Resistance | Applications in Drones |
---|---|---|---|---|---|---|
Carbon Fiber | High | High | Low | High | Moderate | Airframes, booms, propellers |
Aluminum Alloy | Moderate | Moderate | Moderate | Moderate | High | Motor mounts, landing gear, chassis components |
ABS Plastic | Low | Low | Low | Low | High | Enclosures, non-structural components |
The table highlights the trade-offs between different materials. While carbon fiber provides superior strength and stiffness for its weight, it comes at a higher cost. Aluminum alloys offer a more balanced approach, suitable for components requiring robust impact resistance. Plastics are the most cost-effective option, though they are less suitable for load-bearing structural components. The choice of material often depends on the specific drone design, its intended application, and the budget constraints.
Drone Software Development and Programming
The software powering a drone is far more complex than simply controlling its motors. It’s a sophisticated system managing flight stability, navigation, sensor data processing, and communication, all while adhering to safety protocols. The development of this software requires specialized skills and a deep understanding of embedded systems, real-time programming, and potentially artificial intelligence.
Drone software development involves a multifaceted approach, integrating various functionalities to ensure safe and efficient flight operations. This necessitates the use of several programming languages and frameworks, each tailored to specific tasks and hardware constraints. Challenges arise from the need for real-time responsiveness, efficient resource management within the limited computational power of onboard systems, and the integration of diverse sensor data streams. Robustness and reliability are paramount, given the potential consequences of software failure in a flying vehicle.
Programming Languages and Frameworks
Commonly used programming languages in drone software development include C/C++, Python, and increasingly, languages like Rust, known for their memory safety features. C/C++ are favored for their performance and direct hardware access, crucial for real-time control systems. Python, with its extensive libraries for data processing and machine learning, is frequently used for higher-level tasks like mission planning and autonomous navigation. Frameworks like ROS (Robot Operating System) provide a standardized architecture for building complex robotic systems, including drones, facilitating modularity and code reusability. Other frameworks, specific to drone manufacturers or platforms, may also be utilized.
Challenges in Drone Software Development
Developing robust and reliable drone software presents several significant challenges. Real-time constraints necessitate efficient algorithms and code optimization to ensure responsiveness to sensor data and pilot commands. Resource limitations on the drone’s onboard computer require careful memory and power management. The integration of diverse sensors, each with its own data format and characteristics, presents a significant integration challenge. Ensuring software safety and fault tolerance is paramount to prevent crashes or malfunctions. Furthermore, developing software for autonomous navigation requires sophisticated algorithms for path planning, obstacle avoidance, and localization, often involving machine learning techniques. Finally, security is a growing concern, as drones become increasingly interconnected and vulnerable to hacking or malicious control.
Simplified Drone Control System Software Architecture
The following describes a simplified flowchart illustrating the software architecture of a drone control system. Imagine a central control loop receiving data from various sources (GPS, IMU, cameras, etc.). This data is processed to determine the drone’s current state and compared against desired commands (from a pilot or autonomous navigation system). Based on this comparison, control algorithms generate appropriate commands for the motors and other actuators. This loop runs continuously at a high frequency to maintain stable and controlled flight.
[Flowchart Description: The flowchart would begin with a “Data Acquisition” block, encompassing inputs from GPS, IMU (Inertial Measurement Unit), barometer, and other sensors. This feeds into a “State Estimation” block, which uses sensor fusion techniques to determine the drone’s position, orientation, and velocity. Next, a “Control Algorithm” block receives this state information and compares it to “Desired State” inputs (pilot commands or autonomous navigation plan). The difference between these states is used to generate “Actuator Commands” which are sent to the motors and other actuators via a “Command Execution” block. Finally, a “Feedback Loop” connects the “Command Execution” block back to the “Data Acquisition” block, closing the loop and allowing for continuous adjustments based on real-time feedback.]
Drone Integration with Other Technologies: Design Technologies Drone
The synergistic potential of drones is significantly amplified through their integration with other advanced technologies. This integration not only enhances drone capabilities but also unlocks new applications across diverse industries, leading to increased efficiency, improved data collection, and enhanced decision-making processes. This section explores the key integrations driving the evolution of drone technology.
Drone integration with IoT platforms and cloud computing, AI and machine learning, and various industry-specific technologies are reshaping the landscape of various sectors. This integration is fostering innovation and driving efficiency improvements across the board.
Drone Integration with IoT and Cloud Computing
The convergence of drones with the Internet of Things (IoT) and cloud computing creates a powerful ecosystem for data acquisition, processing, and analysis. Drones equipped with sensors can collect vast amounts of data from remote locations, transmitting this information to IoT platforms for real-time monitoring and analysis. Cloud computing provides the necessary infrastructure for storing, processing, and sharing this data, enabling efficient management and informed decision-making. For example, a network of agricultural drones equipped with multispectral cameras can monitor crop health across a large farm, transmitting data to a cloud platform where AI algorithms analyze the data to identify areas needing attention, such as irrigation or fertilization. This allows for precision agriculture, optimizing resource utilization and maximizing yield.
Drone Integration with AI and Machine Learning for Autonomous Operations
AI and machine learning are pivotal in enabling autonomous drone operations. Sophisticated algorithms allow drones to navigate complex environments, make real-time decisions, and perform tasks without human intervention. Computer vision, a subset of AI, allows drones to “see” and interpret their surroundings, enabling obstacle avoidance and precise target identification. Machine learning algorithms, trained on vast datasets, improve the drone’s performance over time, adapting to changing conditions and optimizing flight patterns. An example of this is package delivery drones using AI-powered navigation to autonomously navigate urban environments, avoiding obstacles and delivering packages to designated locations. The algorithms constantly learn and improve their route planning and obstacle avoidance based on the data collected during each delivery.
Drone Integration in Various Industry Applications
The integration of drones with other technologies varies widely depending on the specific industry application. In infrastructure inspection, drones equipped with high-resolution cameras and thermal imaging sensors, integrated with cloud-based data analysis platforms, allow for efficient and detailed inspection of bridges, power lines, and pipelines. In search and rescue operations, drones integrated with thermal cameras and AI-powered object detection can locate missing persons in challenging terrains. Similarly, in environmental monitoring, drones equipped with LiDAR and hyperspectral sensors, integrated with GIS software, create detailed 3D models of landscapes for analyzing deforestation, pollution levels, or wildlife populations. The data collected is then uploaded to a cloud-based platform for analysis and reporting.
Future Trends in Drone Design Technologies
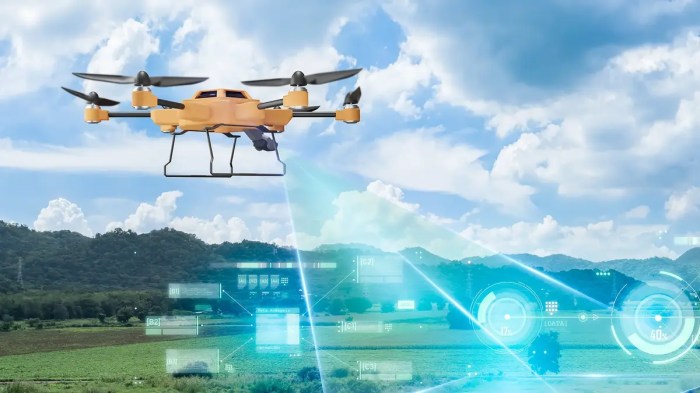
The future of drone technology promises significant advancements across various aspects of design, driven by innovations in materials science, propulsion systems, and artificial intelligence. We can expect to see drones that are smaller, lighter, more efficient, and capable of performing increasingly complex tasks autonomously. This evolution will be shaped by the convergence of several emerging technologies, leading to a new generation of drones with enhanced capabilities and wider applications.
The integration of advanced materials and propulsion systems will be crucial in shaping the next generation of drones. Lightweight yet strong materials, such as carbon fiber composites and advanced polymers, will continue to reduce the overall weight of drones, leading to improved flight times and payload capacity. Simultaneously, advancements in electric propulsion, including the development of more efficient motors and battery technologies, will extend flight durations significantly, enabling drones to undertake longer missions and cover greater distances.
Advancements in Drone Miniaturization and Energy Efficiency
Miniaturization is a key focus, with researchers actively pursuing the development of smaller, lighter drones capable of navigating complex environments with ease. This involves shrinking down essential components without sacrificing performance. For example, the integration of micro-electromechanical systems (MEMS) technology allows for the creation of smaller, more efficient sensors and actuators. In parallel, progress in battery technology, such as solid-state batteries and improved lithium-ion chemistries, is critical in enhancing energy density and reducing weight, ultimately leading to longer flight times and increased operational efficiency. Consider the shift from bulky lithium-polymer batteries to lighter, more energy-dense alternatives – a key factor in enabling the development of smaller, more agile drones like those used for indoor inspection or precise agriculture tasks.
The Role of Artificial Intelligence and Autonomous Flight
Artificial intelligence (AI) is revolutionizing drone autonomy, enabling drones to perform complex tasks without direct human control. AI algorithms enable sophisticated navigation systems, allowing drones to avoid obstacles, plan optimal flight paths, and adapt to changing environmental conditions. For example, AI-powered object recognition allows drones to identify and track specific targets, such as individuals or objects in search and rescue operations, or to precisely apply pesticides in agriculture. Machine learning further enhances autonomy by allowing drones to learn from their experiences, improving their performance over time. This continuous learning capability leads to increasingly robust and reliable autonomous flight capabilities.
Impact of Virtual and Augmented Reality
Virtual Reality (VR) and Augmented Reality (AR) technologies are poised to significantly impact drone development and operation. VR can be utilized for realistic drone simulations, allowing pilots to practice complex maneuvers and emergency procedures in a safe, controlled environment before operating real drones. This enhances training and reduces the risk of accidents during real-world operations. AR overlays digital information onto the real-world view, providing pilots with critical data such as flight parameters, obstacle locations, and target information directly within their field of vision. This enhanced situational awareness improves the efficiency and safety of drone operations, especially in challenging environments. Imagine a pilot using AR glasses to see a real-time thermal map overlaid on their visual feed, assisting in search and rescue missions or infrastructure inspections.
Conclusion
The design and development of drones represent a fascinating confluence of diverse technological advancements. From initial conceptualization using advanced CAD software to the final integration of sophisticated sensor payloads and autonomous flight capabilities, each stage highlights the remarkable progress made in this sector. The future of drone technology promises even greater miniaturization, enhanced autonomy, and expanded applications across numerous industries, shaping a future where aerial platforms play an increasingly pivotal role in various aspects of our lives.
The burgeoning field of design technologies for drones requires a specialized skillset. To truly excel in this area, professionals often pursue relevant certifications to demonstrate competency, and a strong understanding of related software is key. For instance, consider exploring various information technology certifications that cover areas like data analysis and software development, crucial for optimizing drone performance and data processing.
This ultimately enhances the overall design and functionality of drone technologies.
Design technologies in drone development are constantly evolving, pushing the boundaries of what’s possible. A key area impacting similar remote-control systems is the advancement of e collar technologies , which offer insights into precise control and feedback mechanisms. This understanding of remote stimulus and response is directly applicable to improving drone navigation and autonomous operation, ultimately refining design technologies in drone engineering.