Steel technologies underpin modern civilization, from the skyscrapers that define our cities to the vehicles that transport us. This exploration delves into the multifaceted world of steel, examining its production, properties, and applications across diverse industries. We will traverse the entire lifecycle of steel, from raw material extraction to innovative applications and sustainable recycling practices.
This journey will cover various steel production methods, including blast furnaces and electric arc furnaces, analyzing their respective advantages and disadvantages. We will explore the crucial role of alloying elements in tailoring steel’s properties for specific applications and investigate various forming and fabrication techniques, encompassing traditional methods alongside cutting-edge additive manufacturing. Furthermore, we will examine crucial aspects such as corrosion protection, quality control, and the vital role of steel in construction and the automotive industry. Finally, we will peer into the future, considering emerging trends and the ongoing evolution of steel technologies.
Steel Production Methods: Steel Technologies
Steel production is a complex process, encompassing various methods to transform iron ore into the versatile material we know today. The choice of method depends on factors such as the desired steel grade, cost considerations, and available resources. Two primary methods, the blast furnace and the electric arc furnace, form the foundation of steelmaking, each with its own strengths and weaknesses. Beyond these initial stages, the basic oxygen furnace (BOF) and continuous casting play crucial roles in refining and shaping the final product.
Blast Furnace and Electric Arc Furnace Comparison
The blast furnace and electric arc furnace represent distinct approaches to iron and steel production. The blast furnace, a towering structure, utilizes a continuous, high-temperature process to reduce iron ore into pig iron. This pig iron then undergoes further processing to become steel. Conversely, the electric arc furnace (EAF) uses electricity to melt scrap metal and iron ore, directly producing steel.
The blast furnace boasts high production capacity and is well-suited for large-scale operations. However, it is capital-intensive, requires significant energy input, and generates considerable environmental impact due to its reliance on coke (a form of coal) as a reducing agent. The EAF, on the other hand, is more energy-efficient when using significant amounts of scrap metal as feedstock, produces less pollution, and has a lower capital cost. However, its production capacity is typically lower than a blast furnace, and it relies heavily on the availability of scrap metal.
Basic Oxygen Furnace (BOF) Process
The Basic Oxygen Furnace (BOF) is a crucial step in steelmaking, refining the pig iron or molten iron from a blast furnace or EAF into steel. The process involves blowing high-velocity oxygen into molten iron, causing rapid oxidation of impurities such as carbon, silicon, manganese, and phosphorus. These impurities are removed as gases (carbon monoxide, carbon dioxide) or slag (a molten mixture of oxides).
The chemical reactions in the BOF are complex but can be summarized as follows:
C(s) + O2(g) → CO2(g)
Si(s) + O2(g) → SiO2(s)
Mn(s) + 1/2O2(g) → MnO(s)
P(s) + 5/4O2(g) → P2O5(s)
These reactions are exothermic, meaning they release heat, contributing to the high temperature maintained within the furnace. The slag formed during the process floats on top of the molten steel, separating the impurities.
The following table summarizes the key inputs and outputs of the BOF process:
Input | Description | Output | Description |
---|---|---|---|
Molten Iron | From blast furnace or EAF, containing impurities. | Steel | Refined molten iron with reduced impurities. |
Oxygen | High-purity oxygen gas, blown into the molten iron. | Slag | Molten mixture of oxides containing removed impurities. |
Flux | Materials (e.g., lime) added to help form slag and remove impurities. | Gases | Primarily carbon monoxide (CO) and carbon dioxide (CO2). |
Scrap Steel (Optional) | Added to adjust the chemical composition and temperature. | Heat | Exothermic reactions generate significant heat. |
Continuous Casting Process
Continuous casting is a highly efficient method for solidifying molten steel into semi-finished products like slabs, blooms, and billets. Instead of pouring the molten steel into individual molds, continuous casting involves continuously pouring the molten steel into a water-cooled mold, where it solidifies into a semi-finished product. This product is then cut into the desired lengths.
The continuous casting process significantly improves steel quality by minimizing the formation of defects and ensuring a more uniform microstructure. It also dramatically increases productivity and reduces production costs compared to traditional ingot casting methods. The consistent quality and efficiency of continuous casting have made it an integral part of modern steel production.
Steel Alloying and Properties

The properties of steel, a crucial material in countless applications, are significantly influenced by its composition. Alloying, the process of adding other elements to iron-carbon base, allows for precise tailoring of mechanical characteristics to meet specific performance requirements. This section explores the effects of common alloying elements and the process of steel alloy design.
Effects of Alloying Elements on Steel Properties
The addition of alloying elements modifies the microstructure and, consequently, the mechanical properties of steel. Understanding these effects is crucial for selecting the appropriate steel grade for a given application. The following table summarizes the impact of some key alloying elements:
Alloying Element | Effect on Strength | Effect on Ductility | Effect on Corrosion Resistance |
---|---|---|---|
Carbon (C) | Increases strength, especially at higher concentrations. Forms carbides which strengthen the steel. | Decreases ductility as carbon content increases; higher carbon steels are harder and more brittle. | Generally decreases corrosion resistance, particularly in higher concentrations. |
Manganese (Mn) | Increases strength and hardness, improves hardenability. | Reduces ductility slightly, but less so than carbon. | Offers some improvement in corrosion resistance, particularly in combination with other elements. |
Chromium (Cr) | Increases strength and hardness, significantly improves corrosion resistance (stainless steels). | Reduces ductility slightly. | Dramatically increases corrosion resistance, forming a passive chromium oxide layer. |
Nickel (Ni) | Increases strength and toughness, improves ductility and impact resistance. | Increases ductility and toughness. | Improves corrosion resistance, particularly in combination with chromium. |
Steel Alloy Design for Specific Applications
Designing a steel alloy involves a careful consideration of the desired properties and the application’s demands. For instance, high-strength low-alloy (HSLA) steels, commonly used in automotive parts, require a balance of high strength, good weldability, and formability. These steels typically contain small additions of elements like manganese, silicon, copper, and sometimes vanadium or niobium to refine the grain structure and enhance strength without sacrificing too much ductility. The precise composition is determined through extensive testing and simulation to optimize the balance of properties for the intended use, such as ensuring sufficient tensile strength for structural integrity while maintaining the ability to be easily formed into complex shapes during manufacturing. This process often involves computational modelling to predict the material behaviour under various loading conditions.
Impact of Heat Treatment on Steel Microstructure and Properties
Heat treatment significantly alters the microstructure and, therefore, the mechanical properties of steel. Different heat treatment methods achieve varying effects.
Examples of Heat Treatment Methods and Their Effects
Annealing, for instance, involves heating the steel to a specific temperature, holding it for a period, and then slowly cooling it. This process relieves internal stresses, softens the steel, and improves its ductility. Quenching involves rapidly cooling the steel from a high temperature, typically in water or oil. This process traps carbon in solution, resulting in a hard, but brittle martensitic structure. Tempering follows quenching and involves reheating the steel to a lower temperature, which reduces the brittleness and increases toughness. The specific temperature and duration of each stage are carefully controlled to achieve the desired combination of strength, hardness, and toughness. For example, a tool steel might undergo a complex sequence of austenitizing, quenching, and tempering to achieve the necessary hardness and wear resistance, whereas a structural steel might only require annealing for stress relief and improved formability.
Steel Forming and Fabrication
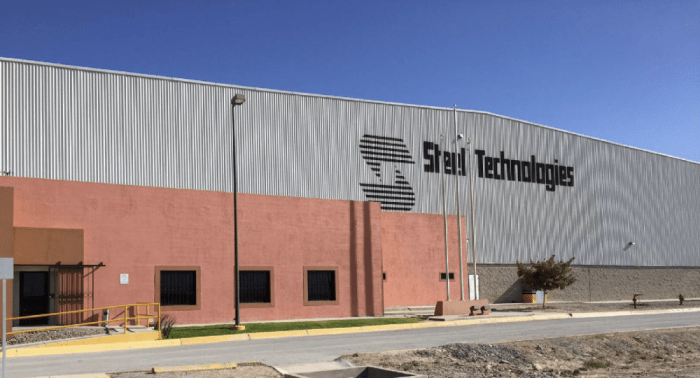
Steel forming and fabrication encompasses a wide range of processes used to shape and join steel components into finished products. The choice of forming and fabrication techniques depends heavily on the desired final shape, mechanical properties, and economic considerations. Understanding these processes is crucial for efficient and cost-effective steel manufacturing.
Comparison of Steel Forming Techniques
Several primary forming techniques exist, each offering unique advantages and disadvantages regarding microstructure and final product characteristics. Rolling, forging, extrusion, and drawing are among the most prevalent.
Rolling: This process involves passing a heated steel billet through a series of rollers to reduce its thickness and increase its length. The resulting microstructure is typically elongated and aligned in the rolling direction, leading to anisotropic mechanical properties (different properties in different directions). Rolled steel products are commonly used in applications requiring high strength and ductility in one direction, such as sheet metal for automotive bodies.
Forging: Forging involves shaping steel by hammering or pressing it into a desired shape. This process results in a refined microstructure with improved strength and ductility compared to casting. The grain structure becomes more homogenous, leading to isotropic properties (similar properties in all directions). Forged components are often used in high-stress applications, such as crankshafts and connecting rods.
Steel technologies are constantly evolving, incorporating advanced processes and materials for enhanced strength and durability. Protecting these innovations requires specialized coverage, which is why understanding the offerings of a technology insurance company, such as technology insurance company , is crucial for businesses in this sector. This ensures that the financial risks associated with research, development, and implementation of cutting-edge steel technologies are mitigated.
Extrusion: In extrusion, a heated steel billet is forced through a die to create a continuous profile of a specific shape. Similar to rolling, the microstructure is often elongated in the extrusion direction. This process is well-suited for producing long, complex shapes such as pipes and structural sections. The final product typically exhibits good surface finish and dimensional accuracy.
Drawing: Drawing involves pulling a steel rod or wire through a die to reduce its diameter and increase its length. This process leads to a significant increase in strength and a reduction in ductility due to the work hardening effect. Drawn steel wires are commonly used in applications requiring high tensile strength, such as cables and springs.
Fabrication Process Design for a Complex Steel Component
Let’s consider the design of a fabrication process for a complex steel component, such as a high-pressure valve body. The valve body requires high strength, corrosion resistance, and precise dimensional tolerances.
Material Selection: A high-strength, corrosion-resistant steel alloy, such as 316 stainless steel, would be suitable. Its superior mechanical properties and corrosion resistance are crucial for the intended application.
Forming Methods: The valve body could be initially formed using forging to achieve the desired shape and microstructure. Forging ensures excellent mechanical properties and homogeneity. Subsequent machining operations would refine the dimensions and create precise features.
Joining Techniques: Welding could be employed to join different parts of the valve body. For example, gas tungsten arc welding (GTAW) or laser beam welding (LBW) would ensure high-quality welds with minimal heat-affected zones, maintaining the integrity of the material properties.
Steel technologies are constantly evolving, incorporating advanced processes and materials for enhanced strength and durability. Protecting these innovations requires specialized coverage, which is why understanding the offerings of a technology insurance company, such as technology insurance company , is crucial for businesses in this sector. This ensures that the financial risks associated with research, development, and implementation of cutting-edge steel technologies are mitigated.
Additive Manufacturing of Steel
Additive manufacturing, also known as 3D printing, is emerging as a promising technology for steel fabrication. This technology allows for the creation of complex geometries and intricate designs that would be difficult or impossible to produce using traditional methods.
Advantages: Additive manufacturing offers the potential for significant design flexibility, reduced material waste, and the ability to create customized parts on demand. It enables the production of lightweight, high-strength components with optimized internal structures.
Limitations: Current additive manufacturing techniques for steel face challenges in terms of build speed, surface finish, and the ability to achieve consistent mechanical properties across the entire component. The cost of the equipment and materials is also a significant factor limiting widespread adoption.
Steel Coatings and Surface Treatments
Protecting steel from the detrimental effects of corrosion and enhancing its performance characteristics are crucial aspects of its widespread application. A variety of coatings and surface treatments are employed to achieve this, each offering a unique balance of protection, cost-effectiveness, and aesthetic appeal. The choice of method depends heavily on the specific application and the desired lifespan of the steel component.
Corrosion Protection Methods
Several methods effectively protect steel from corrosion. These methods differ significantly in their application, longevity, and cost. Understanding the strengths and weaknesses of each approach is vital for selecting the optimal solution.
- Galvanizing: This process involves immersing steel in molten zinc, creating a protective zinc layer that acts as a sacrificial anode. If the coating is scratched, the zinc will corrode preferentially, protecting the underlying steel. Galvanizing offers excellent corrosion resistance, particularly in outdoor environments, and boasts a relatively long lifespan, often exceeding several decades. The thickness of the zinc coating determines the longevity of protection. However, galvanizing can alter the appearance of the steel and may not be suitable for all applications, particularly those requiring high aesthetic standards.
- Painting: Painting is a versatile and widely used method for protecting steel. A variety of paints, including oil-based, water-based, and specialized coatings, are available, each offering different levels of protection and durability. Proper surface preparation is crucial for paint adhesion and longevity. While painting is relatively inexpensive, its effectiveness depends on the quality of the paint and the thoroughness of the application. Regular maintenance, including repainting as needed, is often required to maintain long-term protection.
- Powder Coating: Powder coating involves applying a dry powder coating to the steel surface, followed by curing in an oven. This process produces a durable, smooth, and aesthetically pleasing finish. Powder coatings offer excellent resistance to corrosion, abrasion, and chemicals, making them suitable for a wide range of applications. They are also environmentally friendly, as they produce little to no volatile organic compounds (VOCs). However, powder coating requires specialized equipment and expertise for application.
Protective Coating Application Process
Applying a protective coating to steel involves a systematic process that significantly influences the effectiveness of the final product. Three main stages are involved: surface preparation, coating application, and curing.
Surface preparation is critical for ensuring proper adhesion of the coating. This typically involves cleaning the steel surface to remove dirt, grease, rust, and other contaminants. Methods such as blasting, brushing, and chemical cleaning are commonly employed. The choice of cleaning method depends on the level of contamination and the type of coating being applied.
Coating application techniques vary depending on the chosen coating. For painting, brushes, rollers, or spray guns can be used. Powder coating is applied electrostatically, using specialized equipment. Galvanizing involves immersing the steel in a molten zinc bath. Careful control of the application process is crucial for ensuring uniform coating thickness and quality.
Curing is the final stage in the process, which involves allowing the coating to harden and fully develop its protective properties. For paints, this can involve air drying or oven curing. Powder coatings are cured in an oven at high temperatures. The curing process is essential for achieving the desired durability and performance characteristics of the coating.
Surface Treatments for Enhanced Properties
Surface treatments can significantly enhance the properties of steel beyond corrosion protection. These treatments modify the surface layer of the steel to improve its wear resistance, hardness, or other desired characteristics.
- Nitriding: This process involves diffusing nitrogen into the surface of the steel, increasing its hardness and wear resistance. Nitrided steel components are commonly used in applications requiring high durability, such as engine parts and cutting tools. The increased hardness and resistance to wear extend the lifespan of the component and improve overall performance.
- Hard Chrome Plating: This involves electroplating a layer of chromium onto the steel surface, creating a hard, wear-resistant coating. Hard chrome plating is used in applications requiring high resistance to abrasion and corrosion, such as hydraulic cylinders and machine parts. The thick chromium layer provides excellent protection against wear and tear, extending the operational life of the component.
Steel Recycling and Sustainability
Steel recycling plays a crucial role in mitigating the environmental impact of steel production and promoting a more sustainable future. Its importance stems from the significant energy savings and reduced emissions associated with using recycled steel compared to producing new steel from raw materials. The process itself is remarkably efficient, contributing to a circular economy model for this vital material.
Steel recycling is a multi-stage process that transforms discarded steel into valuable new steel products. This circular approach significantly reduces the environmental footprint compared to using virgin materials.
The Steel Recycling Process
The journey of a discarded steel can to becoming new steel involves several key steps. First, steel scrap is collected from various sources, including demolition sites, manufacturing facilities, and household waste. This collected scrap is then sorted according to its grade and composition, ensuring the quality of the recycled steel. This sorting process is critical for maintaining the desired properties of the final product. Next, the sorted scrap is transported to steel mills for processing. There, it undergoes a series of steps, including shredding and melting, to prepare it for re-use. Finally, the molten steel is refined and cast into new steel products, completing the recycling cycle.
Environmental Impact Comparison
Producing steel from recycled scrap requires significantly less energy and generates fewer greenhouse gas emissions than producing steel from iron ore. A substantial reduction in mining, transportation, and processing is achieved through recycling. Compared to aluminum production, which is energy-intensive, steel recycling offers a more environmentally friendly alternative. Furthermore, steel recycling presents a considerable advantage over plastics, many of which are not readily recyclable and often end up in landfills, contributing to environmental pollution. For example, studies have shown that producing steel from recycled scrap requires approximately 75% less energy than producing it from raw materials, resulting in a corresponding decrease in carbon dioxide emissions. This translates to a considerably smaller carbon footprint and a more sustainable approach to steel production. The environmental benefits are substantial, particularly when compared to the extensive resources and energy consumed in the production of aluminum or the environmental damage caused by the disposal of non-recyclable plastics.
Advanced Steel Technologies
The development of advanced steel technologies has significantly broadened the applications of steel, pushing the boundaries of its performance capabilities across diverse sectors. This progress is driven by the need for stronger, lighter, more durable, and more sustainable materials in industries facing ever-increasing demands. These advancements involve innovative alloying techniques, sophisticated processing methods, and the integration of nanotechnology.
High-strength steel represents a cornerstone of these advancements, offering substantial improvements in strength-to-weight ratio compared to conventional steels. The use of advanced steel alloys further enhances these properties, incorporating specialized characteristics such as high-temperature resistance and superior corrosion resistance. Nanotechnology, in its nascent stages of application, holds immense promise for further refinement of steel’s properties.
High-Strength Steel Applications
High-strength steels are integral to modern engineering, finding widespread use in automotive, aerospace, and construction industries. In the automotive sector, they contribute to lighter vehicle weight, improving fuel efficiency and reducing emissions. High-strength steel components, such as advanced high-strength steel (AHSS) used in car bodies, reduce the overall weight without compromising safety. The aerospace industry leverages high-strength steel’s exceptional strength-to-weight ratio in aircraft components, contributing to improved fuel efficiency and extended flight ranges. Similarly, in construction, high-strength steels enable the construction of taller and more slender structures, maximizing space utilization and minimizing material usage. For example, high-strength steel is frequently used in skyscrapers and long-span bridges.
Advanced Steel Alloys with Enhanced Properties
Beyond high-strength, advanced steel alloys are engineered to exhibit enhanced properties tailored to specific applications. For instance, stainless steels, known for their exceptional corrosion resistance, are vital in chemical processing, medical equipment, and architectural applications. Heat-resistant steels, incorporating elements like chromium and molybdenum, find critical roles in power generation, aerospace propulsion systems, and high-temperature industrial processes. These alloys can withstand extreme temperatures without significant loss of strength or structural integrity. The development of duplex stainless steels, combining austenitic and ferritic microstructures, provides a balance between strength, corrosion resistance, and weldability. These alloys are used in various applications where high strength and corrosion resistance are crucial.
Nanotechnology in Steel Improvement
The integration of nanotechnology offers a novel pathway for enhancing the properties of steel. The incorporation of nanoparticles, such as carbon nanotubes or graphene, into the steel matrix can significantly improve its mechanical strength, hardness, and toughness. These nanoparticles act as reinforcing agents, enhancing the steel’s resistance to deformation and fracture. Furthermore, nanotechnology allows for the precise control of the microstructure and composition of steel, enabling the creation of materials with tailored properties. While still in the early stages of development and widespread industrial implementation, this approach shows considerable potential for future advancements in steel technology. Research is ongoing to fully realize the potential of nanotechnology in improving various aspects of steel production and properties.
Steel Testing and Quality Control
Ensuring the quality and reliability of steel is paramount across diverse industries, from construction to automotive manufacturing. Rigorous testing and quality control procedures are implemented throughout the steel production process to guarantee that the final product meets specified standards and performs as expected. This involves a multifaceted approach encompassing raw material inspection, process monitoring, and finished product evaluation.
Mechanical Property Testing Methods
Several methods are employed to assess the mechanical properties of steel, providing crucial insights into its strength, ductility, and toughness. These tests are vital for selecting appropriate steel grades for specific applications and verifying that the manufactured steel meets the required specifications.
Tensile testing involves subjecting a standardized steel specimen to a controlled tensile force until fracture. The resulting stress-strain curve reveals key properties such as yield strength (the stress at which permanent deformation begins), tensile strength (the maximum stress before fracture), and elongation (a measure of ductility). Hardness testing measures the resistance of a material to indentation. Common methods include Brinell, Rockwell, and Vickers hardness tests, each using different indenters and force applications. The resulting hardness number indicates the material’s resistance to scratching, wear, and deformation. Impact testing evaluates a material’s ability to absorb energy upon impact, indicating its toughness. The Charpy and Izod impact tests are commonly used, measuring the energy absorbed during the fracture of a notched specimen. The results are crucial for assessing the material’s susceptibility to brittle fracture at low temperatures.
Quality Control in Steel Production
Quality control in steel production is a continuous process, starting with the selection and inspection of raw materials like iron ore, coal, and limestone. Chemical composition is analyzed to ensure it aligns with the desired steel grade. Throughout the steelmaking process – from melting and refining to casting and rolling – parameters such as temperature, time, and chemical additions are carefully monitored and controlled. Regular sampling and testing at various stages ensure consistency and adherence to specifications. Finally, finished steel products undergo rigorous testing, including mechanical property tests and dimensional checks, to confirm compliance with quality standards before shipment. Statistical process control (SPC) techniques are often used to monitor process variability and identify potential problems early on. For example, control charts track key process parameters, allowing for timely adjustments to prevent defects.
Non-Destructive Testing (NDT) Methods
Non-destructive testing (NDT) methods are crucial for evaluating the quality of steel without causing damage to the material. These techniques are employed at various stages of production and are particularly important for detecting internal flaws or defects that might compromise the integrity of the finished product. Common NDT methods include: Ultrasonic testing (UT) uses high-frequency sound waves to detect internal flaws like cracks and inclusions. Radiographic testing (RT) utilizes X-rays or gamma rays to create images revealing internal defects. Magnetic particle testing (MT) is used to detect surface and near-surface cracks in ferromagnetic materials. Liquid penetrant testing (PT) identifies surface-breaking defects by allowing a dye to penetrate the crack and then revealing its presence. These methods ensure that only high-quality steel products are released into the market, minimizing the risk of failure in service.
Steel in Construction
Steel’s exceptional strength-to-weight ratio, durability, and versatility make it a cornerstone material in modern construction. From towering skyscrapers to intricate bridges, steel’s properties allow for innovative designs and efficient construction processes, impacting both aesthetics and functionality. This section will explore the various types of steel used in construction, design considerations, and a comparison with alternative building materials.
Types of Steel Used in Construction
Several types of steel are specifically engineered for construction applications, each possessing unique characteristics suited to different structural needs. Structural steel, reinforcing steel (rebar), and stainless steel represent the most commonly used types. Structural steel, typically carbon steel, forms the primary load-bearing elements in buildings and bridges. Reinforcing steel, often featuring ribbed surfaces for improved bond strength with concrete, provides tensile strength to reinforced concrete structures. Stainless steel, known for its corrosion resistance, finds applications in cladding, facades, and other elements exposed to harsh environments. Other specialized steels, such as weathering steel (Corten steel), which develops a protective rust layer, are also utilized for their aesthetic and maintenance advantages.
Design Considerations for Steel Structures
Designing steel structures requires careful consideration of several crucial factors to ensure safety, longevity, and structural integrity. Load-bearing capacity is paramount, necessitating accurate calculations to determine the steel sections needed to withstand anticipated loads, including dead loads (weight of the structure itself), live loads (occupancy, equipment), and environmental loads (wind, snow, seismic activity). Stability is equally critical, requiring consideration of buckling and overall structural behavior under various loading conditions. Corrosion protection is vital for extending the lifespan of steel structures. This often involves protective coatings, such as paints or galvanization, to prevent rust and degradation. Careful detailing and proper fabrication are also essential to minimize stress concentrations and ensure the intended performance of the steel members.
Advantages and Disadvantages of Steel in Construction, Steel technologies
The following table compares the advantages and disadvantages of using steel in construction against concrete and wood, considering factors such as cost, strength, durability, and sustainability.
Feature | Steel | Concrete | Wood |
---|---|---|---|
Strength | High tensile strength, excellent load-bearing capacity | High compressive strength, good in tension when reinforced | Relatively lower strength compared to steel and concrete |
Durability | Long lifespan with proper corrosion protection | High durability, resistant to many environmental factors | Susceptible to rot, insect damage, and fire |
Cost | Can be relatively expensive, depending on steel prices and fabrication costs | Generally less expensive than steel, but costs can vary based on mix design and placement | Generally the least expensive option |
Sustainability | High recyclability rate, but energy-intensive production | High embodied carbon, but can incorporate recycled materials | Renewable resource, but deforestation concerns exist |
Workability | Relatively easy to fabricate and assemble | Requires specialized equipment and skilled labor for placement | Relatively easy to work with using traditional tools |
Fire Resistance | Requires fireproofing for adequate fire resistance | Naturally fire-resistant | Low fire resistance unless treated |
Steel in Automotive Industry
The automotive industry is a significant consumer of steel, relying on its versatility, strength, and cost-effectiveness to produce a wide range of vehicle components. The ongoing drive for improved fuel efficiency and enhanced safety has led to the increasing use of advanced high-strength steels (AHSS) and innovative design strategies. This section explores the crucial role of steel in modern automotive manufacturing, highlighting its contribution to vehicle performance and safety.
The utilization of high-strength steel significantly improves both the fuel efficiency and safety of automobiles. Higher strength-to-weight ratios allow for the design of lighter vehicles, directly reducing fuel consumption. Simultaneously, these stronger steels enhance the structural integrity of the vehicle, improving its ability to withstand impacts and protect occupants during collisions. This improvement in crashworthiness is a critical factor in achieving higher safety ratings. For example, the use of AHSS in the design of vehicle chassis and body structures has demonstrably reduced the severity of injuries in real-world accidents.
High-Strength Steel and Vehicle Lightweighting
High-strength steel alloys, such as dual-phase (DP), transformation-induced plasticity (TRIP), and complex phase (CP) steels, offer superior strength compared to conventional steel grades at similar thicknesses. This allows automakers to use less material while maintaining or exceeding the required structural performance. The reduction in vehicle weight translates to lower fuel consumption, reduced CO2 emissions, and improved overall vehicle performance. Specific examples include the use of ultra-high-strength steel in lightweight body panels and structural components like B-pillars and side sills.
Design Considerations for Steel Automotive Components
Designing steel components for automotive applications necessitates a careful balance between weight reduction and crashworthiness. Finite element analysis (FEA) is extensively used to simulate crash scenarios and optimize component design for maximum energy absorption during impacts. The design process considers factors such as material properties, component geometry, and joining techniques to ensure optimal performance. For instance, strategically placed reinforcements using high-strength steel can improve energy absorption in specific areas of the vehicle structure, like the front and rear crumple zones.
Manufacturing Processes for Steel Automotive Components
Several manufacturing processes are employed to produce steel components for automobiles. These include hot stamping, which involves forming steel at high temperatures to achieve superior strength and formability; cold stamping, a more cost-effective process used for less demanding components; and roll forming, a continuous process for producing long, shaped parts like side rails. Advanced high-strength steels often require specialized forming processes to overcome their higher strength and potentially lower ductility. Laser welding and other advanced joining techniques are used to assemble the various steel components into complete vehicle structures, ensuring high-quality and consistent welds.
Future Trends in Steel Technologies
The steel industry, a cornerstone of global infrastructure and manufacturing, is undergoing a period of significant transformation driven by advancements in materials science, manufacturing processes, and a growing emphasis on sustainability. Future trends are shaped by the need for stronger, lighter, more corrosion-resistant, and more environmentally friendly steel products, all while maintaining cost-effectiveness. This evolution promises to reshape not only the steel industry itself but also numerous downstream sectors reliant on its output.
The development of advanced steel alloys represents a key area of focus. Research efforts are concentrated on improving existing alloys and creating entirely new ones with enhanced mechanical properties, such as higher strength-to-weight ratios, improved ductility, and superior resistance to corrosion and high temperatures. This translates to lighter vehicles, stronger bridges, and more durable infrastructure components.
Advanced Steel Alloys and Enhanced Properties
The pursuit of superior steel alloys is driven by the demand for materials capable of withstanding increasingly demanding operational conditions. For example, research into high-strength low-alloy (HSLA) steels continues, focusing on optimizing their microstructure to achieve exceptional strength while maintaining weldability and formability. Furthermore, significant progress is being made in developing advanced high-strength steels (AHSS) that incorporate innovative microstructures, such as transformation-induced plasticity (TRIP) and twinning-induced plasticity (TWIP) steels, to achieve unprecedented strength and ductility combinations. These advancements find application in the automotive industry, leading to lighter and safer vehicles, and in construction, resulting in more robust and efficient structures. Another example is the development of corrosion-resistant steels, such as duplex stainless steels, which offer a balance of strength and corrosion resistance, making them suitable for applications in harsh environments like offshore structures and chemical processing plants.
Impact of Advanced Manufacturing Technologies
Advanced manufacturing technologies are poised to revolutionize steel production and processing. Additive manufacturing, or 3D printing, allows for the creation of complex steel components with intricate geometries, impossible to achieve through traditional methods. This opens up possibilities for customized designs and optimized performance. Similarly, advancements in robotics and automation are enhancing efficiency and precision in steel production, leading to reduced waste and improved quality control. Digital twin technology allows for the simulation and optimization of steel production processes, predicting potential problems and improving overall efficiency. The integration of artificial intelligence (AI) and machine learning (ML) in steel manufacturing promises further improvements in predictive maintenance, quality control, and process optimization. For example, AI-powered systems can analyze vast amounts of data from sensors and other sources to identify patterns and predict equipment failures, minimizing downtime and improving overall productivity.
Challenges and Opportunities in the Steel Industry
The steel industry faces a number of challenges in the coming years, including the need to reduce its environmental footprint, improve energy efficiency, and meet increasingly stringent regulatory requirements. However, these challenges also present significant opportunities for innovation and growth. The transition to a circular economy, with a focus on steel recycling and reuse, is gaining momentum, driven by environmental concerns and the economic benefits of resource recovery. Developing innovative steel recycling technologies, such as direct reduced iron (DRI) production from scrap, is crucial for reducing reliance on virgin materials and minimizing carbon emissions. Furthermore, the increasing demand for sustainable steel products, produced with reduced carbon emissions, is driving the development of new technologies such as hydrogen-based steelmaking, which promises a significant reduction in greenhouse gas emissions compared to traditional blast furnace methods. The steel industry’s ability to adapt and innovate will determine its success in the years to come, shaping a future where steel remains a vital material for a sustainable and technologically advanced world.
Steel and its Economic Impact
The steel industry plays a pivotal role in the global economy, impacting numerous sectors and national GDPs. Its economic significance is multifaceted, ranging from its direct contribution through manufacturing and employment to its indirect influence on downstream industries reliant on steel products. Understanding this impact requires examining both the global and regional perspectives, as well as the factors that fluctuate steel prices and its overall contribution to economic growth.
Steel’s economic importance stems from its versatility and strength, making it a crucial material across various sectors. The industry itself provides substantial employment opportunities, from mining iron ore and coal to steelmaking, processing, and fabrication. This creates a ripple effect, supporting related industries like transportation, construction, and manufacturing. Furthermore, steel’s durability and cost-effectiveness contribute to infrastructure development and the production of consumer goods, driving economic growth in both developed and developing nations.
Global and Regional Economic Significance of the Steel Industry
The global steel industry is a massive economic engine. Major steel-producing nations like China, India, Japan, and the United States significantly contribute to global GDP through steel production and export. Regional variations exist, reflecting factors such as access to raw materials, energy costs, technological advancements, and government policies. For instance, regions with abundant iron ore reserves and access to inexpensive energy often enjoy a cost advantage in steel production. Conversely, regions with stricter environmental regulations may face higher production costs. The economic impact within each region is substantial, influencing employment rates, trade balances, and overall economic health. Fluctuations in global steel demand directly affect these regions, impacting employment and investment decisions within the industry.
Factors Affecting Steel Prices
Several interconnected factors influence the price of steel, creating a dynamic and often volatile market. Supply and demand are fundamental drivers; high demand coupled with limited supply pushes prices upward, while oversupply can lead to price declines. Raw material costs, particularly iron ore and coal, are significant cost components in steel production. Increases in these raw material prices directly translate to higher steel prices. Energy prices also play a critical role; steelmaking is an energy-intensive process, and fluctuations in energy costs significantly impact production costs and, consequently, steel prices. Furthermore, global economic conditions, geopolitical events, and government policies (such as tariffs and subsidies) can influence steel prices by affecting demand, supply, and production costs. For example, the global financial crisis of 2008 significantly reduced steel demand, leading to a sharp drop in prices.
Steel’s Role in Supporting Various Industries and Economies
Steel underpins countless industries and economies worldwide. The construction industry relies heavily on steel for buildings, bridges, and infrastructure projects. The automotive industry uses steel extensively in vehicle manufacturing, impacting both the cost and performance of vehicles. The energy sector uses steel in pipelines, power plants, and wind turbines. Manufacturing, packaging, and countless other sectors rely on steel for tools, machinery, and components. This widespread reliance makes steel a critical factor in economic growth and development. A strong steel industry translates to a strong manufacturing base, supporting jobs and contributing to a nation’s overall economic competitiveness. Conversely, a weak steel industry can hinder economic progress across numerous sectors.
Closure
The remarkable versatility and enduring strength of steel have solidified its position as a cornerstone of global industry and infrastructure. From the foundational processes of steelmaking to the innovative applications driving technological advancement, this overview has highlighted the depth and breadth of steel technologies. Understanding the intricacies of steel production, alloying, forming, and application is crucial for continued innovation and sustainable development across numerous sectors. The future of steel is bright, driven by ongoing research and the development of advanced materials and manufacturing processes.